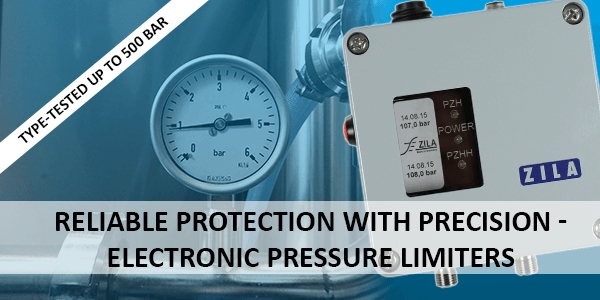
- Written by ZILA GmbH
Reliable protection with precision - Electronic pressure limiters
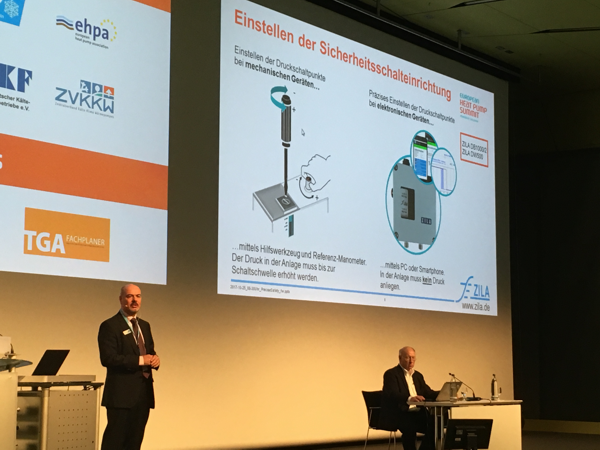
Refrigeration systems and heat pumps must be designed and manufactured in such a way that possible hazards to people, properties and the environment can be eliminated. For this reason, appropriate protective devices must be provided to monitor critical limits. Precise setting and monitoring of these limit values even facilitates optimised machine and plant design.
Protective devices for pressure limitation and pressure relief
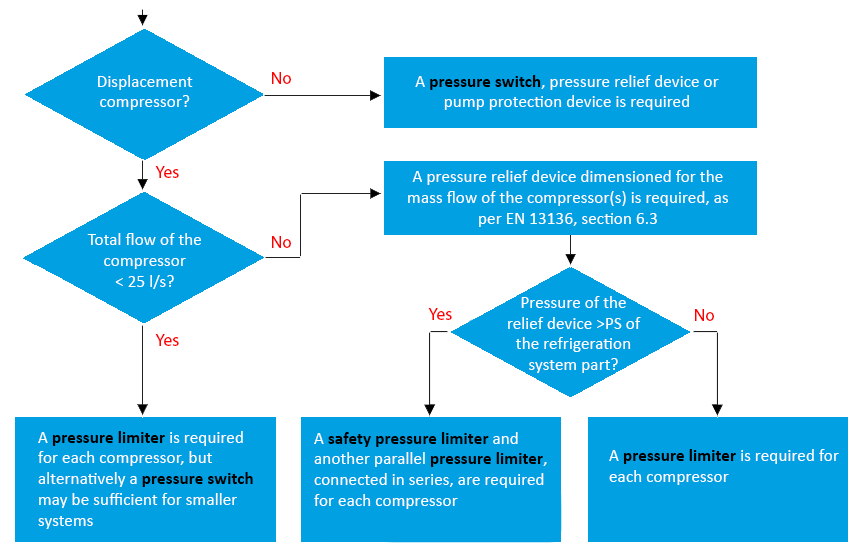
Protective devices are special components with safety functions for monitoring limit values. Such devices include safety valves, bursting discs, buckling rods and fusible plugs providing for pressure relief and safe shutdown of the pressure generator. While protection against excessive pressure is primarily for personal and plant safety, a reduction in pressure can lead to incorrect plant operation and is usually also an indication of a leakage. Therefore, minimum pressure limitation should also be considered with respect to machine efficiency and, above all, environmental protection. When and which exact measures are to be taken is determined by corresponding directives, such as the Machinery Directive and the Pressure Equipment Directive as well as by subject-specific regulations. For refrigeration systems and heat pumps, the EN 378 directive is to be applied. To get a quick overview of what EN 378 is about, please check out the picture above.
Safety switching devices for pressure limitation
Depending on the direction of action, there are devices for limiting to falling pressure (low or minimum pressure limiting) and devices for protection against excessive pressure (high or maximum pressure limiting). These safety switching devices must be designed in such a way that the machine or plant is always brought back to safe conditions, even in the event of a error. Moreover, such devices must be submitted to a type examination. In this context, the manufacturer of the device must prove to a recognised inspection and certification body that the device is perfectly constructed and operates properly without any faults.
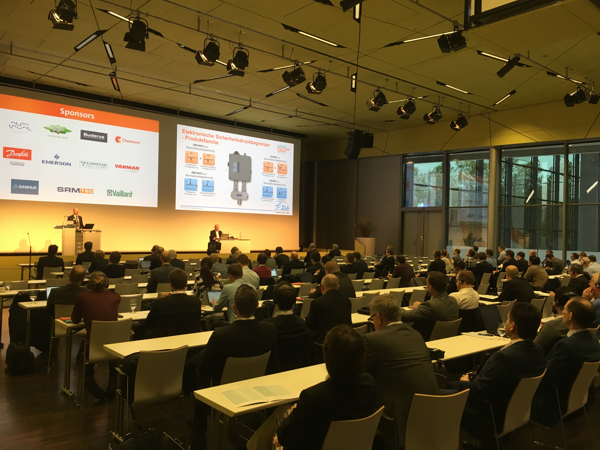
Depending on the machine and plant situation, there are three types of safety switching devices, which can be used for pressure limitation. Furthermore, pressure switches can be equipped with different unlocking methods, according to the functions required by the system. Below you will find a table of the devices used for protection against rising pressure. For pressure limitation to falling pressure, the "H" is replaced by an "L" in the device identification, e.g. PZL for the type-tested minimum pressure limiter.
PSH, PZH, PZHH | Description |
![]() |
|
![]() |
|
![]() |
|
The switch points of the pressure relief device must be set in such a way that a shutdown of the pressure generator can be ensured before the pressure relief device is triggered. If it is possible to set the switch points precisely, the 10 % difference between the safety device setting and the pressure relief device setting may be reduced accordingly. This makes it possible to optimise the machine design and the selection of components.
With conventional mechanical switching devices, the pressure switch point is usually set with an adjustment spindle, using a screwdriver or by a rotary knob and a reference manometer. In this process, the pressure in the system must be carefully approached up to the switching threshold. Electronic pressure limiters, in contrast, are very simple, highly accurate and quickly adjustable.
Electronic safety pressure limiters
ZILA offers a range of devices for pressure limitation, according to the direction of action and function, which, depending on the model, combines a pressure switch, pressure limiter and a safety pressure limiter in one device. The model DB-1000/2 includes a pressure limiter and a safety pressure limiter (PZH + PZHH or PZL + PZLL), while the DW-500 combines a pressure switch and a safety pressure limiter (PSH + PZHH or PSL + PZLL). As there are no moving parts, apart from the safety relays, and thus, hardly any mechanical wear and tear occurs, the electronic devices offer a high long-term stability and a long service life. Compared to conventional mechanical limiters, switch point settings as well as tests of the switching function in a depressurised state can be done very easily on the machine, but also in advance, using our PC software or an Android app.
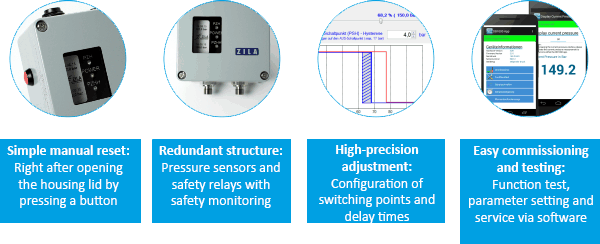
High reliability due to error-proof design
Safety devices must function faultlessly and reliably in every situation. For the electronic safety pressure limiter, on the one hand, this is achieved by its redundant setup and configuration and, on the other hand, by its error-proof device design.
As shown in the figure below, the device basically consists of two mutually monitoring microcontrollers, the two sensor cells and the safety relays. One million switching cycles are guaranteed for the safety relays under nominal load. Besides that, a pressure value is provided to the user as a 4...20 mA signal, so that the system pressure can be monitored and logged at any time.
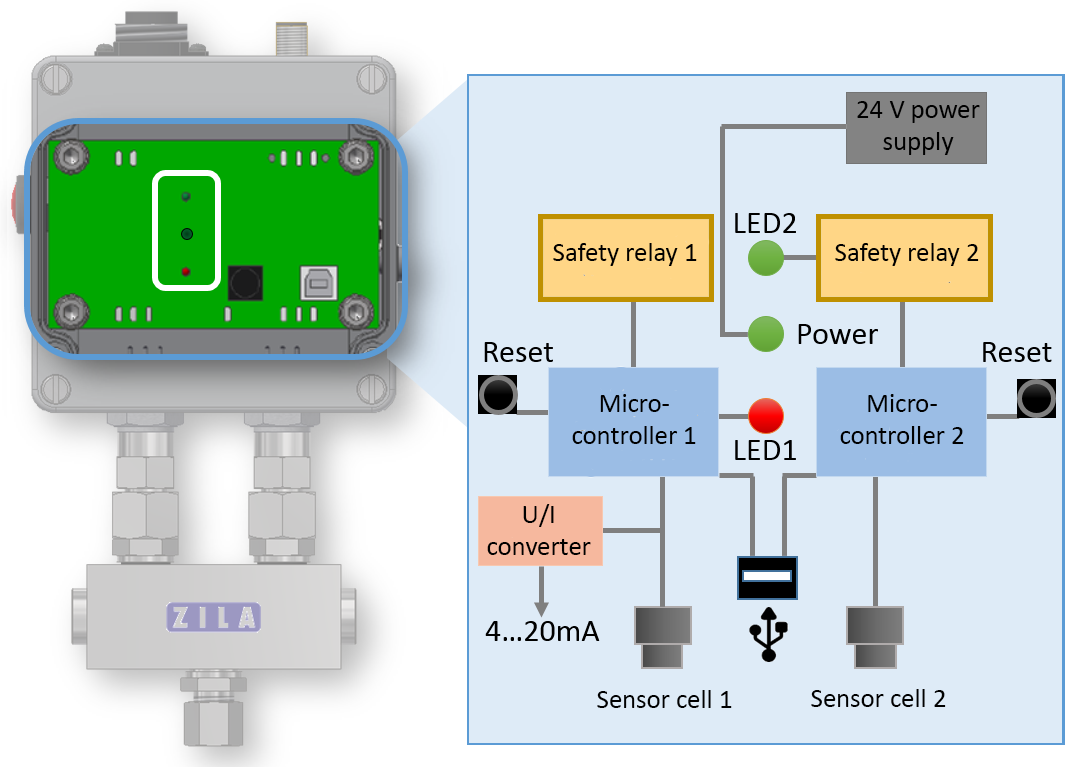
The type-tested devices are error-proof, which means, that even if two errors occur independently from each other, it is ensured that the device continues to operate safely or that the output relay is switched off reliably. This is achieved by special circuitry measures and additional monitoring functions in the device. For example, in the DB-1000/2, the pressure limiter (PZH) and the safety pressure limiter (PZHH) use the "external" pressure sensor for a reciprocal comparison of the measured values. In this way, sensor defects can be detected immediately. Furthermore, there are components independent from the microcontroller (hardware watchdog, monoflop and comparator) in order to monitor time sequences and the operating voltage constantly. This hardware design is supported by the device software, which also includes plausibility checks of the memories and the microcontroller command set, besides extensive cyclically called test routines for all safety-relevant hardware components.
Maximum media compatibility & fast, precise switching behaviour due to electronic pressure cells
The diversity of ZILA safety devices for monitoring and limiting pressure in liquids, gases and vapours requires maximum media compatibility as well as reliable pressure measuring cells, allowing a fast and precise response to critical situations. The electronic pressure sensors in the DB-1000 and DW-500 use a stainless steel membrane for pressure recording. This means that the devices can be used for all stainless steel-compatible media, including flammable media, without any problems.
The devices are approved for a nominal pressure range of up to 500 bar and can thus also be used for CO2 applications in the transcritical range. Thanks to their modular design, it is possible to select the most suitable measuring cell for the application, which, in turn, offers overload protection against pressure peaks of 2.5 to 4 times the nominal pressure. The pressure values of the two sensors are recorded and compared every 5 milliseconds. In order to filter out individual pressure peaks, switching delays of 0.1 to 1 second can be set. The switch or reset points can be set with an accuracy of 0.1 bar. All of these factors make stable and robust pressure monitoring very well possible, with respect to the plant requirements.
Easy commissioning and testing of the safety functions with our software
Fast and accurate setting of the pressure limiter with our free PC software or app not only ensures maximum safety, but also significantly reduces the time and effort required for commissioning the plant concerned and testing its safety functions.
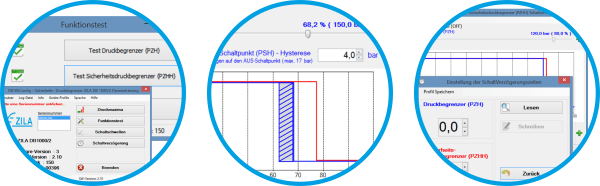
With the intuitive software, you can read out your device settings, configure pressure switch points and carry out function tests. All changes are logged. Additionally, these settings can be saved in the software and thus transferred to other devices conveniently.
The electronic safety pressure limiter from ZILA offers new possibilities in machine and plant design, due to its exact and fast limit value setting, high switching accuracy and its versatility even at high pressures and in difficult media. All in all, the DB-1000's integrated self-test functions and its long service life reduce costs and effort, compared to mechanical devices.
Author: Frank Wiedmann, Managing Director of ZILA GmbH in Suhl, Germany, responsible for Sales and Technology
More information and related links
Site map: Pressure monitoring
Product page: Electronic safety pressure limiter DB-1000/2
Product page: DW500 Safety pressure limiter with pressure switch functionality