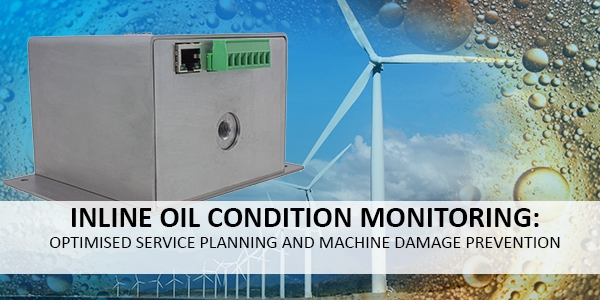
- Written by ZILA GmbH
- font size decrease font size increase font size
Inline oil condition monitoring: Optimised service planning and machine damage prevention
This lubrication with oil prevents machine parts from contact and wear. Other important functions of oil include heat dissipation and protection against corrosion.
However, the oil quality deteriorates over time as the chemical composition of the lubricant changes, so that it no longer possesses the required qualities to operate the machine in question. Factors that can lead to degradation of the oil condition are:
- High temperatures inside the machine
- Frequent load changes during operation
- Contamination with other liquids (e.g. water)
- Wear
In order to keep the oil in the machine as long as possible, its properties are modified by additives. However, in most applications, it must be considered that the oil still has to be replaced regularly. This prevents machine and equipment damage and, in the end, also saves costs, as it does not result in machine downtime or maintenance expenses. If the date for the oil change can be forecasted exactly and service calls can be planned efficiently, there is great potential for cost and time savings, compared to other maintenance strategies.
Predictive maintenance and its connection to optimised service planning
When it comes to maintenance and servicing of machines and plants, a wide variety of approaches and strategies are used. However, the fundamental goal for every plant operator is to maintain the performance of the required resources constantly.
The so-called 'Breakdown maintenance' involves a high risk of failure or even a serious machine damage. Since it is difficult to plan resources, such as personnel and material for maintenance, this is done reactively. Reactive resource planning, in turn, often results in major disadvantages in terms of machine downtimes and service costs. Additionally, safety-relevant requirements for certain system components may not be observed, which is why this form of maintenance has already been replaced by other, more proactive methods (so-called 'Preventive maintenance').
Preventive maintenance can be distinguished into the following methods:
Time-based maintenance follows fixed service intervals. Filters, seals, bearings and the oil itself are replaced within self-defined service periods. The advantage of this method is that the intervals are based on empirical values and thus wear parts can be replaced rather earlier than too late in order to achieve an optimum machine condition. In this way, machines and plants are well-protected against breakdowns, while service and procurement measures can be planned in advance. However, this strategy is disadvantageous in terms of service costs, as components may be replaced too early, too often or without any reason.
With condition-based maintenance, the current degree of wear of a plant component can be determined, so that conclusions about future necessary maintenance measures can be drawn. Therefore, the properties of oil samples are continuously analysed in a lab. Although this oil condition analysis in the laboratory generates higher costs prior to maintenance, service measures can be planned more effectively and critical machine components will be replaced at the right time, so that optimum plant protection can always be ensured.
The predictive maintenance strategy represents a targeted enhancement of condition-based maintenance. For this reason, both strategies share the following similar goals:
- Prevention of machine damage and breakdowns
- Optimum resource and service planning
- Perfectly suitable for fluids, such as oil
Necessary maintenance measures are derived from the oil quality and a predictable (prospective) course of wear. This prediction is based on evaluated sensor data and the maintenance information determined from this data. This has the great advantage that identifying the optimum service time and, with that a high degree of planning reliability lead to attractive cost savings and careful use of resources.
Breakdown maintenance |
Time-based maintenance |
Condition-based maintenance |
Predictive maintenance |
|
Plant protection |
no | yes | yes | yes |
Predictability | no | yes | yes | yes |
Wear reserve | yes | no | yes | yes |
Costs | no | no | no | yes |
Continuous oil condition monitoring for oil quality determination
Oil condition analysis provides reliable information about the quality of the examined oil aleady at an early stage, and thus, also about the condition of a machine. In comparison to other methods, this saves a lot of time. The following graph illustrates the progression of machine damage over time and the advantage of monitoring the oil chemistry.
Additives delaying the wear of lubricants
If we look at the composition of oils, we can see that they essentially (75-99%) consist of a base oil, such as mineral or synthetic oil.
The rest of the base oil (1-25%) is made up of additives, optimising its key performance aspects, so that the final product delivers the optimum performance for the intended application.
Turbines for water, steam and wind
Depending on the design of the rotor blades, wind turbines are exposed to high loads and vibrations at their bearings. This also increases wear, which causes the oil to age more quickly. Depending on the location, corrosion on the bearings can also be an aging factor. This mainly refers to turbines near the coast or in offshore areas. Another challenge when selecting the right oil for turbines in particular, is that formation of harmful deposits should be prevented as far as possible. For this reason, it must be ensured that the oil's wear protection properties are maintained, even if water penetrates. Otherwise, foaming can occur, as trapped air bubbles only have little time to escape from the oil sump, due to the high flow rate.
In water and steam turbines, the operating conditions change permanently, with regard to temperature. This is because the turbines usually run 24/7. The condition of the oil is therefore constantly deteriorating, due to corrosion and oxidation.
Stationary engines
Oil for stationary engines, such as gas engines, is subjected to completely different demands as a result of the use of acid gases. Frequently arising difficulties mainly include ash deposits in the combustion chamber and corrosive halogen compounds or acidic substances in the gas itself. This greatly shortens the service life of the oil because the high ash content and the increasing acid load will cause wear and deposits in the long term.
Transformers
Due to the ever-increasing demands on technology, transformers are expectred to work more and more efficiently. With that, the temperatures, voltages and general demands the transformer oil is exposed to, also increase significantly. This, in turn, often leads to excessive loads, making it necessary for plant operators to modify the base oil with additives, and thus, improve its properties. That is why the use of anti-wear additives can prevent abrasion of two colliding metallic surfaces and valve sticking, for example.
The same applies to soot deposits and other contamination. If there is an increased proportion of antioxidants in the oil, it can also withstand higher loads; this prevents corrosion and stops the lubricating film from tearing off.
Measuring methods for determining typical oil condition parameters
With the help of the latest measuring methods and equipment, important parameters for the oil condition (e.g. oxidation, nitration, water content, etc.) can be determined at the lab. Below we will explain some of these methods in more detail.
The ICP method as a form of atomic spectroscopy is used to detect wear metals, contamination and additives in the oil. This method is based on the fact that energised atoms emit a certain amount of electromagnetic radiation, which then provides information about the chemical composition of the used oil.
The viscometer is a device for measuring the viscosity in order to determine the resistance of a fluid to forced movement. In this way, it is possible to give information about the flow behaviour of liquid substances, in our example about oil. To find out more about this measuring method and our viscometer, please click here: FluidIX Lub-VDT
The FTIR spectroscopy belongs to the infrared spectroscopies and is applied more and more in the oil condition analysis to determine the changes of used oil compared to fresh oil. This comparison can be made because different molecules absorb infrared light to different degrees at certain wavelengths, depending on the type of oil. A signal shift within spectral bands then indicates how much the oil has aged.
Advantages of our oil condition sensor FluidIX Lub-6
With the new oil condition sensor FluidIX Lub-6 for direct integration into a machine or plant, ZILA GmbH opens up a variety of new possibilities for plant operators. Continuous monitoring of the oil condition is possible thanks to multi-value recording and the convenient setting of limit values. Discover now which technology is used to achieve this and which other advantages our sensor offers in terms of operation and economic efficiency of a plant.
The technology
The FluidIX Lub-6 works on the basis of the so-called NDIR technology (non-dispersive infrared technology), which principally works in a similar way as the already described FTIR spectroscopy. The oil sample is also exposed to infrared radiation; however, the decisive advantage, compared to the FTIR spectroscopy, is that only part of the IR spectrum is registered. This means that, only those areas that show an aging effect are observed with the help of wavelength filters.
Predictive oil change in machines and plants
In the past, the breakdown maintenance strategy was often applied, where downtime was inevitable. Today, this approach has been almost completely abandoned, as downtimes are to be prevented for reasons of economic efficiency. This process is supported by the NDIR technology, which is basically a more compact version of FTIR spectroscopy. Due to this innovative technology, our sensor can be applied as an inline solution and is therefore perfectly suited for real-time oil condition monitoring.
The sensor permanently provides useful information on various parameters (e.g. oxidation, water content, additive content (phenols), etc.) which, from quality point of view, can be compared with those of laboratory. On the one hand, this facilitates the determination of the optimum time for an oil change in a machine or plant, and, on the other hand, ensures optimum utilisation of the wear reserve.
In this way, the FluidIX Lub-6 makes an essential contribution to organised, predictable service planning and maintenance.
Easy integration of the FluidIX Lub-6 into existing systems and plants
The following picture shows the simple integration of our sensor into the oil circuit of a system. A connection to the machine control can be established via digital signals or Modbus TCP.
Simple commissioning and operation via web interface
Commissioning and operation of the oil condition sensor FluidIX Lub-6 can be carried out conveniently via a graphical user interface accessible from a computer. All configurations and sensor settings, such as limit value and measuring interval time settings, can be made via this web interface. It is also possible to display the measurements graphically, from which a trend and the corresponding maintenance measures can be derived at an early stage. Another comfort function is that the sensor acts as a data logger, which means that information about the previous sensor configuration can still be retrieved at a later point in time.
Summary
With our oil condition sensor FluidIX Lub-6, the service and maintenance effort can be reduced significantly and, as a result, the service life of the system will be extended.
Moreover, downtimes, procurement and disposal costs are always kept low, thanks to the FluidIX Lub-6.
Should you require more information about this product, you will find it on the following product page: Oil condition sensor FluidIX Lub-6
Prices and availability
Do you have any questions or require specific consultation for your application? We will be pleased to prepare an individual, non-binding offer and advise you on your application.
Please do not hesitate to contact us now, using the following contact options:
Phone: +49 (0) 3681 86-7300
Email: This email address is being protected from spambots. You need JavaScript enabled to view it.
Contact form.
Our experienced sales team is looking forward to your enquiry!